WELDING TABLES WITH FUME EXTRACTION
Find the Perfect Workspace for Manual Welding
Prioritize worker health and safety with welding tables with built-in welding fume extraction. High-quality all-in-one manual welding stations from VentBoss are easy to set up, easy to use, and keep weld fumes away from the breathing zone. These units combine heavy-duty construction, powerful backdraft weld fume extraction, and plug-and-play operation for maximum safety, convenience and productivity.
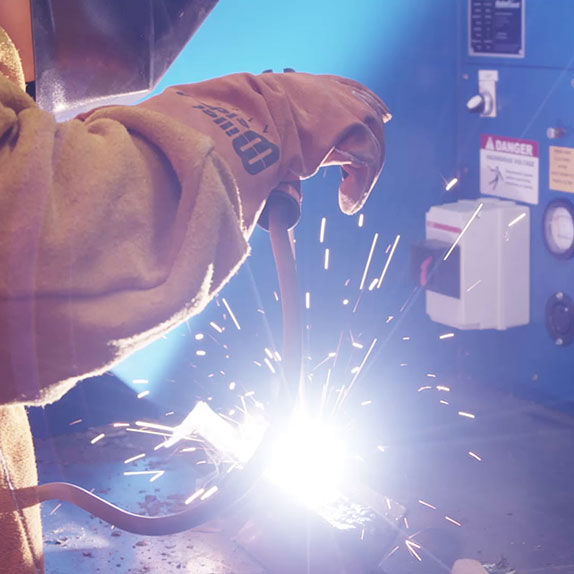
VENTBOSS: ALL-IN-ONE WELD BOOTHS WITH BACKDRAFT EXTRACTION
A welding table with built-in fume extraction saves space and provides maximum convenience for welders: just connect to power and compressed air, place your weldment on the work surface, and start welding. With the VentBoss Series 200 workstations, getting your fabrication shop or weld school up and running has never been easier. These units are ideal for stationary manual welding. The VentBoss 200 Series comes standard with:
- Backdraft system with high-performance blower to keep weld fumes out of the breathing zone (up to 2000 CFM)
- Compressed air filter cleaning for maximum filter life
- 2-layer spark arrestance to keep sparks out of the filter chamber
- Acoustic silencing to minimize noise and ensure operator comfort
- Heavy-duty, all-steel construction
- Built-in power and LED lighting
With a generous 48” wide by 30” deep worksurface, the VentBoss S220 is a great option for weld schools and small shops.
Need more workspace? The VentBoss S230 gives you a 60” x 30” weld table surface for larger weldments or training applications.
FIND YOUR WELDING APPLICATION
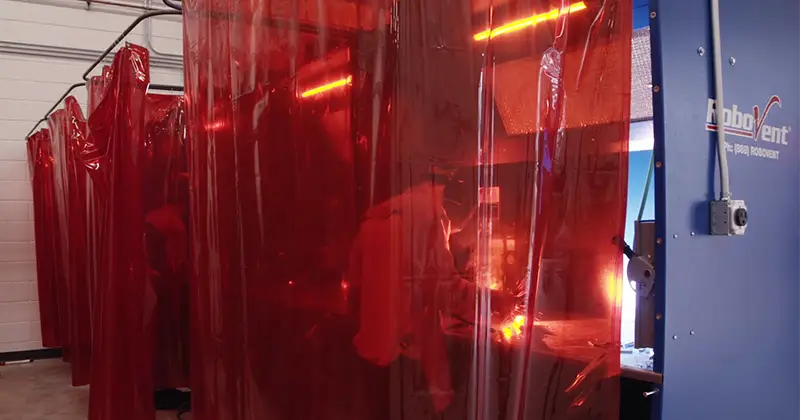
Welding School
As welding schools increase their enrollment and build new facilities, weld fume collection must be a priority. Welding tables with built-in fume extraction are a flexible and simple solution for your welding classroom. Students can practice welding in comfort and safety as they learn their craft.
See it in action:
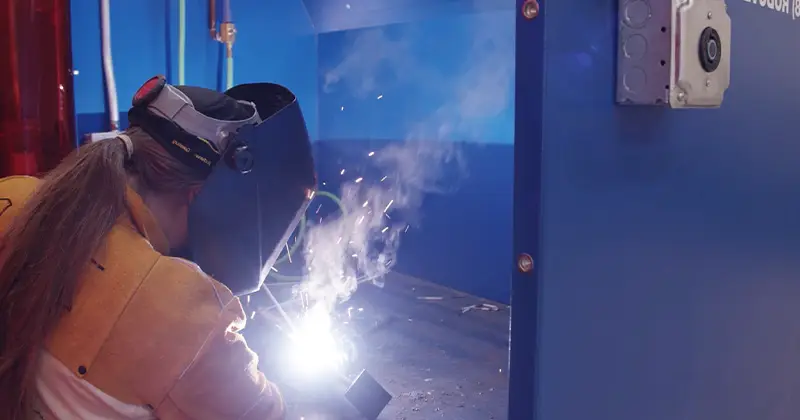
Fabrication Shops
Fabrication shops of all sizes can benefit from the versatility and simplicity of a welding table with integrated fume extraction. Whether you need a single weld station or a whole row, welding tables can be set up fast and moved when needed. And with built-in weld fume extraction, these all-in-one welding stations keep welders safe and shops in compliance.
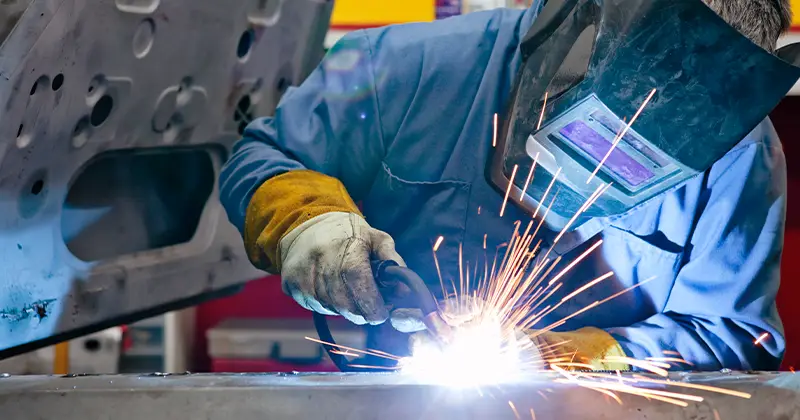
Automotive Repair
Car repair workshops often need welding for repairs and modifications of small parts. They require effective fume extraction to keep the environment safe for both the mechanics and any clients present. A welding table with built-in fume extraction fits easily into the shop environment without requiring complicated ductwork or a separate dust collector.
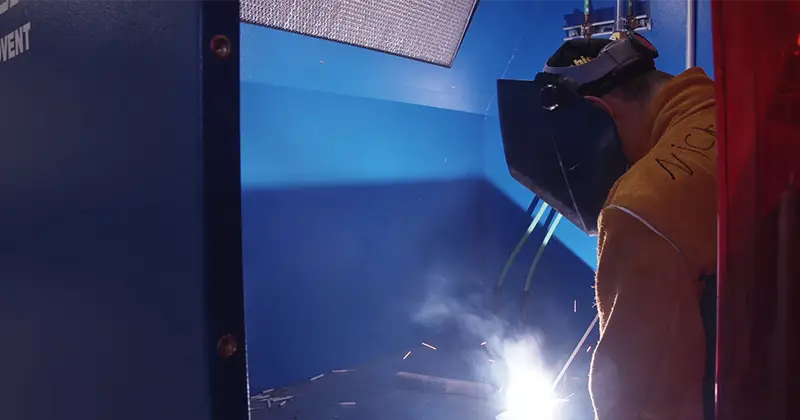
Maintenance Shops
Many large institutions have their own in-house maintenance units, where welding might be a regular requirement. From factories to hospitals, universities, and even large commercial complexes, these in-house maintenance units may require welding to repair damaged parts, seal or join pipes, fix broken tools and furniture, and more. A welding table or booth with built-in fume extraction is an easy and space-saving option to support in-house welders.
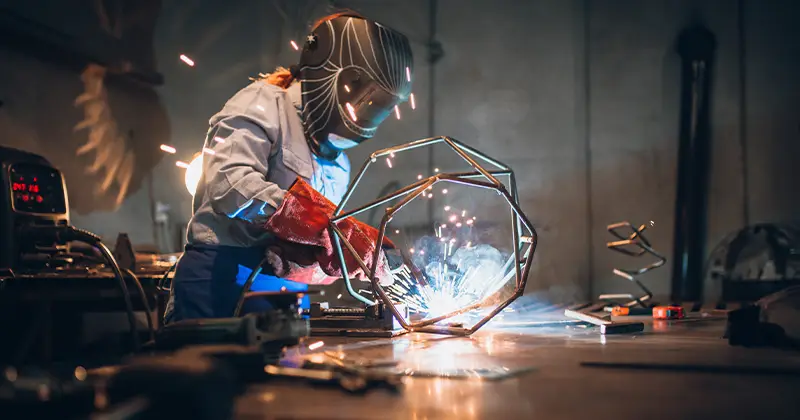
Art Studios
Artists working with metals often require welding as part of their craft. Even though these might be smaller scale compared to industrial applications, the health and safety of the artist are still critical. Art schools and studios need to provide a space for metal artists to practice their craft and create new art pieces. An all-in-one welding booth is the perfect solution for the working artist or art student.
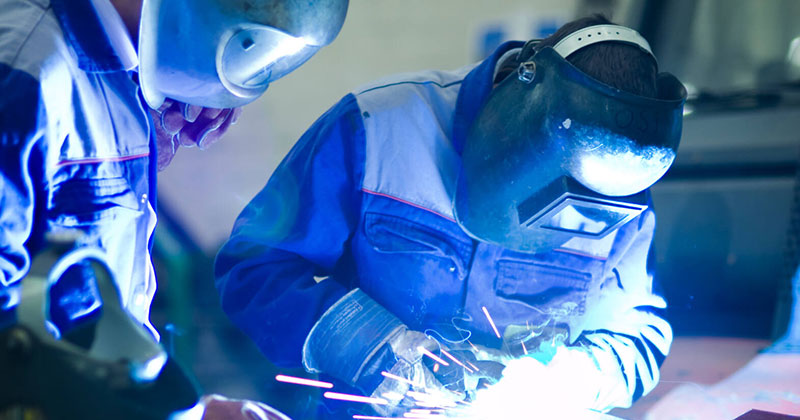
Maker Spaces
Maker spaces are popping up everywhere, and welding is one of the most popular applications for members. These communal spaces provide tools and equipment for creators, artists, hobbyists, and entrepreneurs to collaborate and bring their ideas to life. Welding stations with built-in fume extraction provide a safe space for prototyping, art and design projects, home improvement projects, automotive part repair, robotics, and more.
FREQUENTLY ASKED QUESTIONS ABOUT WELDING TABLES WITH FUME EXTRACTION
Welding Table
What kind of maintenance do welding tables with fume extraction require?
Welding tables with built-in fume extraction systems are usually simple to maintain and operate. However, they do require regular maintenance to ensure that they function optimally and provide a safe working environment. Be sure to follow all maintenance guidelines in the user manual for your specific weld table. Here’s a rundown of the typical maintenance tasks:
- Change filters: Filters must be changed regularly as they become loaded. The filter changing schedule will depend on the volume of weld fume produced and the type of filters used. A compressed air filter pulsing mechanism can extend the life of weld table air filters.
- Clean spark traps: If the system comes with built-in spark arrestance, the spark control system must be cleaned regularly to prevent buildup of grime.
- Empty dust tray/containment: The weld table may come with a dust tray that needs to be emptied regularly or a particulate clean-out area that must be swept or vacuumed out.
- Clean air intake and outlets: Clean the air intakes and outlets to prevent buildup of grime. The intake in particular needs regular cleaning to prevent clogging with larger particles, spatter or slag and ensure optimal airflow.
- Motor/blower maintenance: Fans or blowers used to create negative pressure and pull in fumes might require cleaning, lubrication, or, in some cases, replacement parts.
What is the difference between a backdraft table and a downdraft table?
Backdraft tables and downdraft tables are both designed to capture and extract fumes and particulates produced during welding and similar processes. The primary difference lies in the direction in which they extract those fumes. Backdraft tables pull weld fumes up and away from the source, while downdraft tables pull fumes and dust down through perforations or grates in the work surface. For welding fume extraction, a backdraft table is generally preferred over a downdraft table. This is because weld fumes naturally rise due to the heat involved in the process. Backdraft tables capture these rising fumes more effectively by pulling them horizontally away from the welder. When using downdraft tables, some of the weld fume often escapes upward out of the capture zone, allowing fume to accumulate in the breathing zone and escape the weld booth into the larger facility. Backdraft tables do a better job of keeping weld fume away from the welder’s face for superior welding safety and visibility. Downdraft tables, however, are often preferred for the heavier particulate produced by manual cutting and grinding.
How does a welding table with backdraft fume extraction work?
All-in-one welding booths integrate a welding table with a weld fume extraction system. A backdraft table is designed to capture welding fumes by pulling them away horizontally from the welder’s work area. It then filters the air before returning clean air to the facility. Here’s how it operates:
- Table Design: The welding table typically has a solid flat surface for work. Along the back or side of the table, there’s a raised extraction area, often equipped with slots, grates, or perforations.
- Rising Fumes: As welding commences, the heat causes fumes to rise. Given their natural upward trajectory, they start to move toward the extraction area.
- Extraction System: Behind the perforated back or side area, there’s an extraction system comprised of fans or blowers. This system creates negative pressure, effectively pulling the fumes toward and through the perforated area.
- Filtration: Once the fumes are pulled into the system, they pass through one or more filters that capture particulates.
- Cleaned Air Recirculation: After filtering, the cleaned air is recirculated back into the workshop, ensuring energy efficiency, especially in environments where heating or cooling is essential.
What are the benefits of weld tables with built-in fume extraction?
All-in-one welding booths offer significant advantages for manual welders for many applications. They are also a cost-effective option for weld shops since they eliminate the need for a separate dust collection system. Welding tables with a built-in welding fume extraction system, such as the VentBoss S220 and S230, provide a plug-and-play solution that makes weld fume collection simple. Welders don’t need to worry about the exact placement of the welded piece on the table, and they don’t need to continually readjust a fume arm—they just place the piece on the work surface and weld. The backdraft welding fume extractor pulls weld fumes up and away from the breathing zone, keeping welders safe and facilities in compliance. Weld tables with fume extraction benefits include:
- Simplicity and ease of use
- Worker safety
- Cost efficiency
- Space savings
When should a welding table with built-in fume extraction be used?
Welding tables with integrated backdraft extraction systems can be used for any type of manual welding, including MIG, stick and flux-core welding or manual resistance welding or laser welding. A weld table with built-in fume extraction is a great choice for smaller weldments that can be placed on a work surface. All-in-one welding booths are great options for weld schools, small fabrication shops, and any environment supporting individual manual welders. Learn more about weld table selection.