THE COMPLETE GUIDE TO WELDING
FUME EXTRACTION SYSTEMS:
HOW (AND WHY) TO KEEP YOUR FACILITY AIR CLEAN AND SAFE
CHAPTER THREE: GENERAL PRINCIPLES OF WELD FUME CONTROL
Weld fume controls must be put into place to prevent welders from breathing in harmful fumes and to prevent fumes from propagating through the facility. Weld fume control may include a combination of ventilation, fume extraction and filtration, and personal protective equipment (PPE)—e.g., a powered air-purifying respirator (PAPR). Engineering controls such as ventilation and/or fume extraction and air filtration must be attempted before resorting to PPE as a solution for weld fume protection.
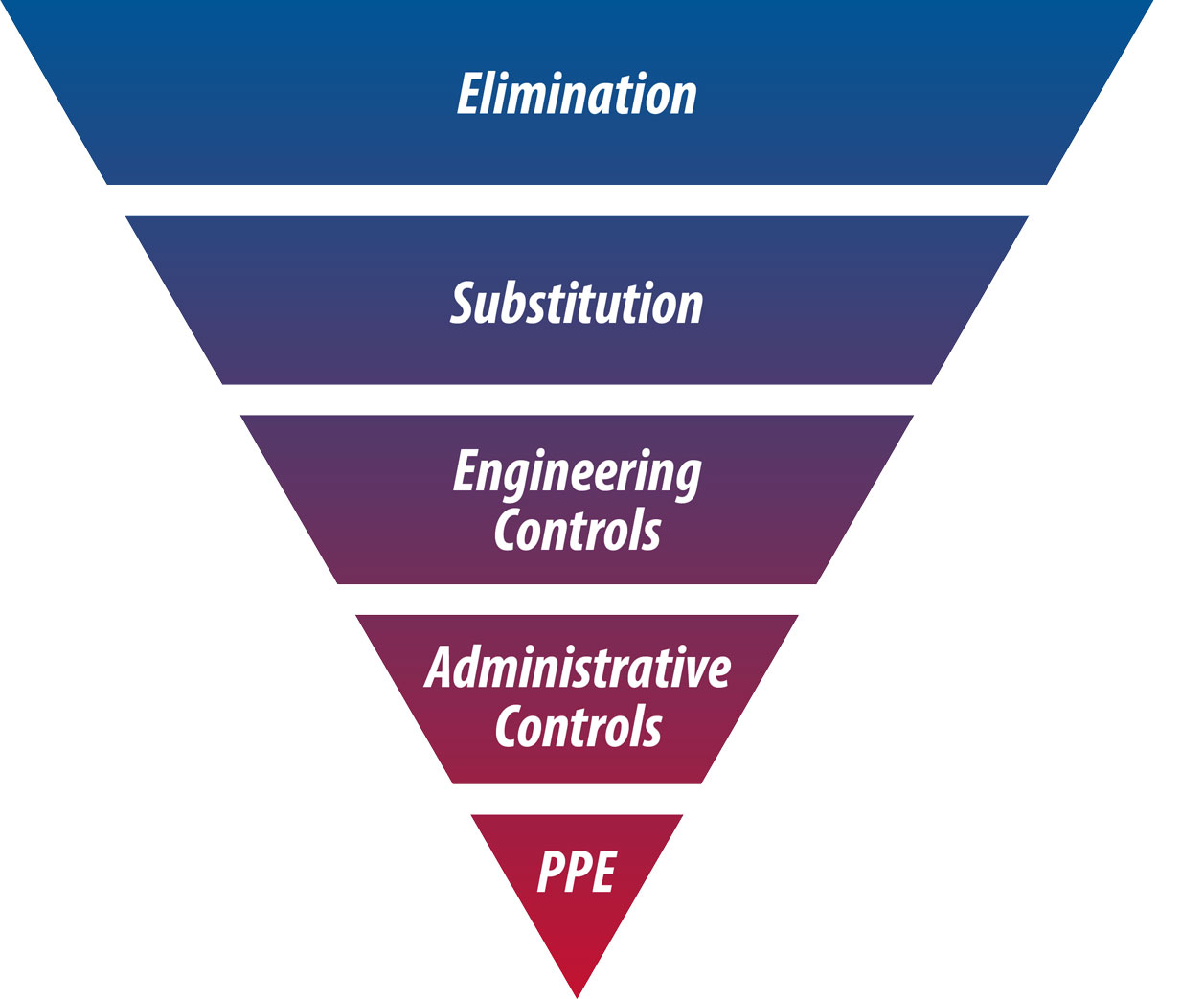
What is the best method for controlling weld fumes?
Generally speaking, a source capture system using air filtration is the preferred method for collecting weld fume for manual welding. A source capture system keeps weld fume out of the breathing zone and prevents it from contaminating the rest of the facility. Filtration systems are preferred over exhaust systems because they prevent contaminants from polluting the environment and keep warmed or cooled air inside the facility, reducing energy waste.
What is dilution ventilation?
Dilution ventilation is a type of ventilation system that is used to control indoor air quality by diluting or reducing the concentration of contaminants in the air. It works by introducing fresh outdoor air into the space, which mixes with the indoor air and dilutes any contaminants that may be present. Dilution ventilation is often used to control odors, fumes, and other air pollutants that are generated by industrial processes. Dilution ventilation systems can be natural (using windows, doors, and other openings to bring in outdoor air) or mechanical (using fans, blowers, and other equipment to bring in outdoor air).
How much ventilation is required for welding?
If relying on natural or mechanical ventilation for weld fume control, OSHA requires a minimum rate of ventilation of 2,000 cubic feet per minute (CFM) per welder, unless local exhaust hoods are used or PPE is provided. The ventilation system should be designed to provide a minimum of six air changes per hour (ACH) in the space where welding is being performed. This means that the entire volume of the space should be replaced with fresh air at least six times per hour. The room change rate and CFM requirements may vary depending on the type and volume of fumes produced; it is important to ensure that ventilation is adequate to keep weld fume exposure below the PEL.
The amount of fresh air that must be brought into a space through a dilution ventilation system for welding will depend on the size of the space, the type of welding being performed, and the concentration of the welding fumes that are being generated. It is important to consult with a qualified engineer or industrial hygienist to determine the appropriate ventilation rate for a specific welding application.
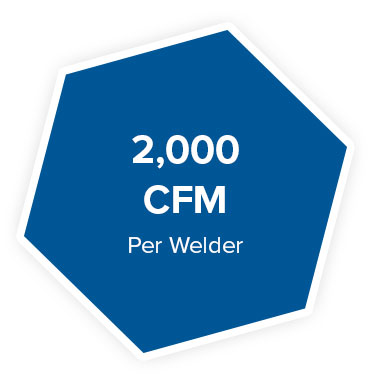
When can NATURAL ventilation be used for weld fume control?
Natural ventilation (e.g., windows, doors, passive venting) is usually not adequate for welding operations. OSHA regulations allow the use of natural ventilation only if:
- welding is not done in a confined area;
- the welding area has at least 10,000 cubic feet of air per welder (roughly 22’ x 22’ x 22’);
- the ceiling height is not lower than 16 feet; and
- cross ventilation is not blocked by equipment, partitions or structural barriers.
When can EXHAUST ventilation be used for weld fume control?
A general exhaust ventilation system may be appropriate in spaces where:
- overall emissions are low;
- emissions are evenly distributed throughout the space and cannot be easily contained; and/or
- workers are not working in the immediate vicinity of the emission source.
Can you exhaust weld fume to the outdoors?
In the U.S., EPA regulations strictly limit the amount of weld fumes that can be exhausted to the outside. The National Emission Standards for Hazardous Air Pollutants (NESHAP) is one of the regulations that specifically applies to welding activities. This standard sets limits on the amount of hazardous air pollutants (HAPs) that can be emitted from manufacturing operations, including welding. HAPs include emissions that contain cadmium, chromium, lead or nickel in levels ≥ 0.1% by weight and/or manganese in levels ≥1% by weight. Weld fume, especially from welding methods that use a consumable weld wire or welding rod, will typically fall under this standard. If welding emissions are exhausted to the outside, you must conduct a Fugitive Emission test to ensure that weld fume emissions do not exceed allowable levels under NESHAP.
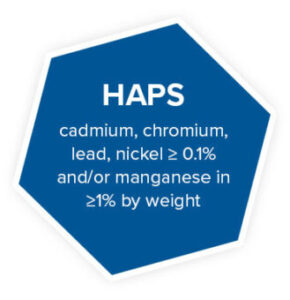
How does industrial air filtration work?
Industrial air filtration removes contaminants from the air and returns clean, filtered air to the facility or to the outdoors. Industrial air filtration systems may use mechanical, electrostatic or chemical filtration methods to remove contaminants. For weld fume, mechanical filtration–such as a cartridge dust collector–is most commonly used to remove the particulate created by the welding process. Chemical filtration (e.g., activated charcoal adsorption) may be required to remove gaseous emissions.
Cleaned air may be returned to the facility (if certain conditions are met) or vented to the outdoors. An air filtration system for welding and other industrial contaminants usually uses a dust collector or wet collection system to filter contaminated air; the HVAC system alone is not adequate to provide filtration for weld fumes and other manufacturing emissions. An air filtration system may be used for either general (ambient) or local (source capture) air filtration.
What is the difference between air filtration and ventilation?
Air filtration is the process of removing contaminants from the air, while ventilation is the process of exchanging indoor air with outdoor air in order to maintain a healthy and comfortable indoor environment.
- Air filtration systems work by passing the indoor air through a series of filters that are designed to remove various contaminants, such as dust, pollen, mold spores, and other particulates. These systems can be used to improve the air quality in a building or a specific room, and are often used in hospitals, schools, and other environments where air quality is a critical concern. Air filtration systems are also used to filter dangerous contaminants and emissions out of air in industrial environments.
- Ventilation systems, on the other hand, work by introducing fresh outdoor air into a building and expelling stale indoor air. These systems can be used to maintain a consistent indoor air quality and to reduce the build-up of pollutants that can be harmful to human health. Ventilation systems are commonly found in residential, commercial, and industrial buildings, and can be either natural (e.g. open windows) or mechanical (e.g. fans, ducts).
When should air filtration be used for welding?
Air filtration systems are recommended for weld fume extraction and control in most circumstances. It is difficult to adequately control welding fumes and keep weld fume out of the breathing zone in high-production welding through ventilation alone. In addition, air filtration prevents contaminants from being released into the atmosphere, which is better for the environment and may be required by EPA clean air regulations (depending on the type and volume of particulate generated). When air is returned to the facility, air filtration can also improve energy efficiency and reduce strain on the HVAC system by reducing the volume of outdoor makeup air that must be heated or cooled.
Why can’t I just use the HVAC system to filter weld fumes?
The HVAC system by itself is generally not adequate for weld fume filtration. Welding fumes are made up of very small particles that can be difficult to filter out using standard heating, ventilation, and air conditioning (HVAC) systems.
- The particles in welding fumes are typically much smaller than the pores in the filters used in HVAC systems, which means that they can easily pass through the filters and be recirculated into the air. Increasing the filtration capabilities (e.g., filter MERV rating) for the entire HVAC system to capture this small particulate is both cost-prohibitive and energy inefficient.
- Particulate that is captured by the HVAC filters will build up and decrease the efficiency of the system. HVAC systems are not designed with large amounts of static pressure, and filter build up will result in poor efficiency and frequent filter changes.
- An HVAC system is designed to turn over all of the air for a space on a regular basis. The air change rate (ACR) is generally not adequate for industrial air filtration.
- In addition, the HVAC system is not designed to remove fume from the breathing zone, which means that workers are still exposed to dangerous weld fume before it enters the HVAC system.
Instead, a specialized air filtration system, such as a fume extractor (dust collector), should be used to effectively remove weld fumes from the air. An industrial dust collection system is designed to handle the large volume of emissions created by welding and other industrial processes. The system should be designed to keep weld fume away from workers. Weld fume is most commonly captured using either an industrial dust collector (dry filtration) or a wet filtration system (wet scrubber).

What is a dust collector?
A dust collector is a type of air filtration system that is used to remove dust and other particulate matter from the air. Dust collectors are commonly used in industrial settings to improve air quality and reduce the risk of explosions and fires caused by dust accumulations. There are several types of dust collectors, including mechanical dust collectors (e.g., cyclone, baghouse, and cartridge dust collectors), which use physical filters to remove dust from the air, and electrostatic dust collectors, which use an electrostatic charge to attract and capture dust particles. Cartridge-style dust collectors are by far the most commonly used type for welding and fabrication.
What kind of dust collector is used for weld fume?
Cartridge dust collectors, such as RoboVent Senturion or RoboVent Spire, are an optimal choice for most welding operations due to their range of filter media options (including high-efficiency filters), smaller size per CFM, and energy efficiency. A cartridge-style dust collector typically consists of a series of cylindrical filter cartridges made of pleated dry filter media that are installed inside a housing. As air flows through the cartridges, the particulates are captured on the surface of the filters. The clean air is then released back into the environment, while the contaminants are collected in a container or disposed of in some other way. Cartridge dust collectors are effective at removing a wide range of particulates, including dust, fumes, smoke, and other airborne contaminants. Filter cartridges come in a range of filter ratings (MERV ratings) for the collection of dry particulate of different sizes. Some cartridge collectors can also be equipped with activated carbon after-filters for the collection of gaseous emissions.
TALK TO AN EXPERT
Want to learn more? Talk to a dust, mist and fume expert today by filling out the fields below.