DUST-CREATING PROCESSES IN PHARMACEUTICAL AND NUTRACEUTICAL PRODUCTION
There are many different solid dosage processes, each with their own dust-creation concerns. Some of these processes include:
- Tablet Pressing
- Capsule Filling
- Powder Batch Mixing/Milling
- Granulation (Wet and Dry)
- Pelletizing and Spheronization
- Fluidized Bed Processes
- Drying processes
- Weighing and Packaging
Related Resources
DUST COLLECTION CHALLENGES FOR THE PHARMACEUTICAL AND NUTRACEUTICAL INDUSTRIES
The pharmaceutical and nutraceutical industries face several challenges when it comes to dust control. The exact risks and challenges depend on the ingredients and processes used.
- Nuisance dust: Many of the dusts created in the production of vitamins, protein powders and other nutraceuticals are not especially toxic or dangerous, but that doesn’t mean dust control isn’t important. Nutraceutical dust can still create health problems—such as lung irritation and aggravation of asthma symptoms—when inhaled. Some nutraceuticals can also trigger allergic reactions in susceptible employees, which can get worse over time with continued exposure. Uncontrolled dust of any type is also a housekeeping and sanitation consideration.
- Hazardous/high-potency pharmaceutical dust: If manufacturing processes create dust with Active Pharmaceutical Ingredients (APIs), more stringent controls will be needed to prevent workers from being exposed. Many pharmaceutical dusts are toxic when inhaled, even in small quantities. And any exposure to medications outside of the normal doctor-prescribed channels is a health concern for employees. Employees exposed to uncontrolled pharmaceutical dusts may have significant side effects, interactions with drugs they are taking, or dangerous allergic reactions. High-potency drugs may require extra-special care to prevent both inhalation and exposure to skin and mucus membranes, even in small amounts.
- Water vapor or solvents: Some pharmaceutical compounding and manufacturing processes create water vapor, solvent vapor or moisture-laden dusts. This can create special challenges in dust collection. Hygroscopic dusts absorb moisture in the air that makes them heavier and stickier. These dusts are harder to pulse off of filters and can cause excessive filter clogging.
- Combustible dusts: Many of the dusts created by pharmaceutical and nutraceutical production are highly combustible. That means they can generate an explosion when allowed to concentrate in the air or inside a dust collection machine. Special care must be taken when collecting combustible dusts to minimize the risks of an explosion inside the dust collector.
- Cross-contamination concerns: Cross-contamination is a particular concern in the pharmaceutical and nutraceutical industries. Dust that is not properly controlled may escape enclosures and contaminate other production lines. This can lead to sanitation and safety concerns, including the risk of dangerous allergic reactions from cross-contamination.
DUST CONTROL REGULATIONS FOR THE PHARMACEUTICAL AND NUTRACEUTICAL INDUSTRIES
The pharmaceutical and nutraceutical industries are highly regulated, with many different standards for every stage of the production process, from sanitizing to packaging. The most relevant regulations for dust control fall into one of two categories: nuisance dusts and hazardous chemicals. Pharmaceutical and nutraceutical manufacturers also have to follow OSHA and NFPA standards for combustible dusts.
- Nuisance dusts: Many nutraceutical dusts fall under the OSHA definition of “nuisance dusts,” which are regulated under the general particulate matter concentration limits set by OSHA. The general limit for “Particulates Not Otherwise Regulated” (PNOLs) is 15 mg/m3 (8-hour TWA limit) for total particulate and 5 mg/m3 for respirable particulates. Employers must also follow general Housekeeping standards (OSHA 1910.22, Walking-Working Surfaces) to prevent accumulation of dust on surfaces.
CONSIDERATIONS IN SELECTING A DUST CONTROL SOLUTION FOR PHARMACEUTICAL AND NUTRACEUTICAL DUST
When designing a dust control solution for pharmaceutical and nutraceutical dusts, engineers will take several factors into consideration. Questions include:
- What are the human health hazards associated with the dust? Does it contain an API? What is the PEL for the dust?
- What are the physical characteristics of the dust? How much dust is produced?
- Does the process keep dust fairly contained (such as in a hood or cabinet), or is it more open?
- Is the dust combustible? What are the combustion risks present in the environment in which it is produced?
- What is the moisture level of the dust? Are water vapor or solvents present in the air?
- Does the process produce dangerous chemical vapors, gases or volatile organic compounds (VOCs) that must be controlled along with the dust?
DUST CONTROL SOLUTIONS FOR THE PHARMACEUTICAL AND NUTRACEUTICAL INDUSTRIES
RoboVent offers robust and innovative dust, fume and odor collection solutions for the vitamin, nutraceutical and low-potency pharmaceutical industries.
Dust control solutions for pharmaceutical and nutraceutical dusts may have several elements.
- Source capture: It is usually best to capture pharmaceutical and nutraceutical dust as close to the source as possible to prevent propagation throughout the facility. Processes that can be enclosed under a hood or in a cabinet can be ducted directly to a dust collector for efficient source capture and filtration.
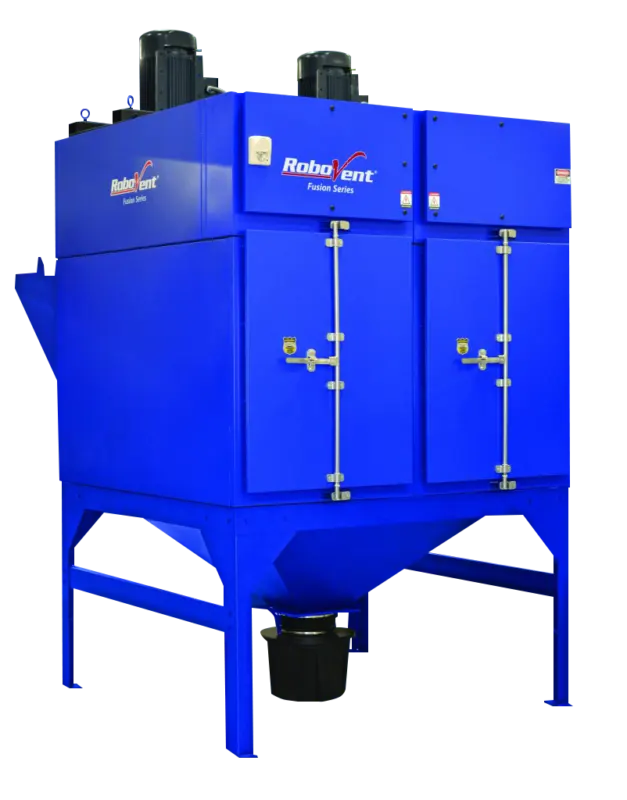
CONTACT US
Contact one of our industrial dust experts to gain the advantage against dust-generating processes and applications.